The Quality Control Life Cycle
The quality control life cycle is an ongoing cycle of planning, monitoring, assessing, comparing, correcting, and improving products or processes. It is designed to improve the quality of a product or process through continuous reinvention. Quality control is used to develop systems that ensure that the goods and services customers receive meet or exceed their expectations.
Quality control both verifies the delivery of good quality and identifies gaps and failures that need to be addressed within the process. Ultimately, it is a process that continuously evolves within the production process.
PDCA (Plan, Do, Check, Act)
PDCA (plan–do–check–act or plan–do–check–adjust) is a four-step management method used in business to control and continuously improve processes and products. It is also known as the Deming circle/cycle/wheel, Shewhart cycle, control circle/cycle, or plan–do–study–act (PDSA). Another version of this PDCA cycle is OPDCA. The added "O" stands for observation or, as some versions say, "Grasp the current condition."
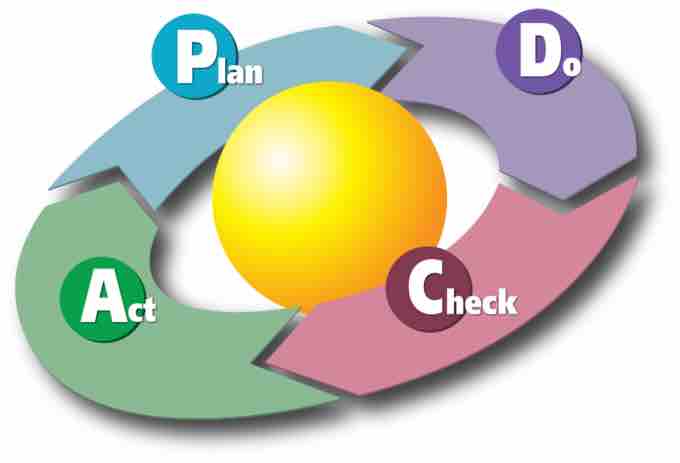
PDCA cycle
Plan, Do, Check, Act
The Four Steps
- Plan: In this step of the quality control cycle, a business establishes the objectives and processes necessary to deliver results in accordance with the expected output (the target or goals).
- Do: In this step, a business implements the plan, executes the process, and makes the product. It also collects data for charting and analysis to be used in the following "check" and "act" steps.
- Check: A business then compares the actual result against the expected result to find any differences.
- Act/Adjust: After comparing results, a business takes corrective actions on any significant differences between actual and expected results. In this step, the business analyzes the differences to determine their root causes, then determines where to apply changes that will improve the process or product.
It is important to keep in mind that this quality control process is continuous and specifically designed to improve the quality of business processes on an ongoing basis. The theory underlying this is the scientific method, where observations are made and hypotheses generated, which are then tested in the next cycle.