Extractive Metallurgy
Extractive metallurgy is the practice of removing valuable metals from an ore and refining the extracted raw metals into a purer form. The field is an applied science, covering all aspects of the physical and chemical processes used to produce mineral-containing and metallic material. The practice of extractive metallurgy almost always involves contributions from other scientific fields, such as analytical chemistry and mineralogy. Sometimes extractive metallurgy produces a finished product, but more often it produces a form that requires further physical processing.
The field of extractive metallurgy encompasses many specialty sub-disciplines, each concerned with various physical and chemical processes that are steps in an overall process to produce a particular material. These specialties are generically grouped into the categories of mineral processing:
- hydrometallurgy
- pyrometallurgy
- electrometallurgy
Mineral processing
Mineral processing manipulates the particle size of solid raw materials to separate valuable materials from materials of no value. Usually, particle sizes must be reduced to efficiently separate valuable materials. Physical properties of valuable materials can include density, particle size and shape, electrical and magnetic properties, and surface properties.
Since many size reduction and separation processes involve the use of water, solid-liquid separation processes are part of mineral processing. In order to dissolve an ore in an aqueous solution, it is often necessary to break the large chunks into smaller pieces, thereby increasing the surface area and the rate of dissolution. It is further possible to break up only ores that are easily crushed, thus allowing them to be dissolved at a much faster rate than those remaining in large chunks.
Hydrometallurgy
Hydrometallurgy describes the process of extracting metals from ores using aqueous solutions. The most common hydrometallurgical process is leaching, which involves the dissolution of the valuable metals into the aqueous solution. After the solution is separated from the ore solids, the solution is often subjected to various processes of purification and concentration before the valuable metal is recovered.
The solution purification and concentration processes may include precipitation, distillation, adsorption, and solvent extraction. The final recovery step may involve precipitation, cementation, or an electrometallurgical process. Sometimes, hydrometallurgical processes may be carried out directly on the ore material without any pretreatment steps. Often, the ore must be pretreated by various mineral processing steps and sometimes by pyrometallurgical processes. Here, the coordination chemistry and solubility of the compound can become very important, as one attempts to precipitate a mineral (metal) of interest over the other metals in the solution or attempts to selectively leach one desired mineral over the others present in the sample.
Pyrometallurgy
Pyrometallurgy involves high temperature processes where chemical reactions take place among gases, solids, and molten materials. Solids containing valuable metals are reacted to form intermediate compounds for further processing or converted into their elemental or metallic state. Processes that produce molten products are collectively referred to as smelting operations. The energy required to sustain the high temperature pyrometallurgical processes may come entirely from the exothermic nature of the chemical reactions taking place, usually oxidation reactions. Often, however, energy must be added to the process by combustion of fuel or, in the case of some smelting processes, by the direct application of electrical energy.
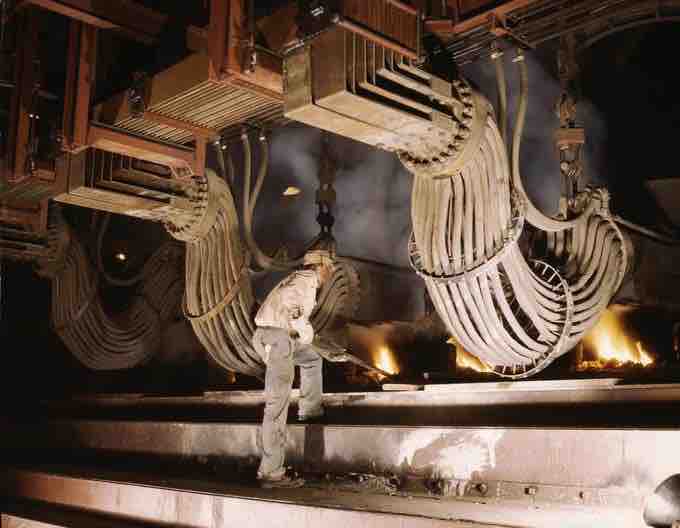
Smelting furnace
High temperatures are often required to melt the ores and metals that come out of mining operations.
Electrometallurgy
Electrometallurgy involves metallurgical processes that take place in some form of electrolytic cell. The most common types of electrometallurgical processes are electrowinning and electro-refining. Electrowinning is an electrolysis process used to recover metals in aqueous solution, usually as the result of an ore having undergone one or more hydrometallurgical processes. The metal of interest is plated onto the cathode, while the anode is an inert electrical conductor. Electro-refining is used to dissolve an impure metallic anode (typically from a smelting process) and produce a high purity cathode. The scope of electrometallurgy has significant overlap with the areas of hydrometallurgy and (in the case of fused salt electrolysis) pyrometallurgy.