Steelmaking Overview
Steelmaking is the second step in producing steel from iron ore. In this stage, impurities such as sulfur, phosphorus, and excess carbon are removed from the raw iron, and alloying elements such as manganese, nickel, chromium, and vanadium are added to produce the exact steel required.
Modern steelmaking processes are broken into two categories: primary and secondary steelmaking. Primary steelmaking uses mostly new iron as the feedstock, usually from a blast furnace. Secondary steelmaking uses scrap steel as the primary raw material. Gases created during the production of steel can be used as a power source.
Primary Steelmaking
Basic oxygen steelmaking is a method of primary steelmaking in which carbon-rich molten pig iron (the iron created in the blast furnace) is made into steel. Blowing oxygen through molten pig iron lowers the carbon content of the alloy and changes it into low-carbon steel. The process is referred to as "basic" because of the pH of the refractories and the calcium oxide and magnesium oxide, which line the vessel to protect against the high temperature of molten metal.
Secondary Steelmaking
Secondary steelmaking is most commonly performed in an electric arc furnace. The furnace consists of a refractory-lined vessel, which is often water-cooled and covered with a retractable roof. It is through this vessel that one or more graphite electrodes enter the furnace. Once the furnace is charged with scrap metal, meltdown commences. The electrodes are lowered onto the scrap, an arc is struck, and the electrodes are set to bore into the layer of shred at the top of the furnace. Once the electrodes have reached the heavy melt at the base of the furnace and the arcs are shielded by the scrap, the voltage is increased and the electrodes raised slightly, increasing the power to the melt. Oxygen is blown into the scrap, combusting or cutting the steel, which accelerates scrap meltdown.
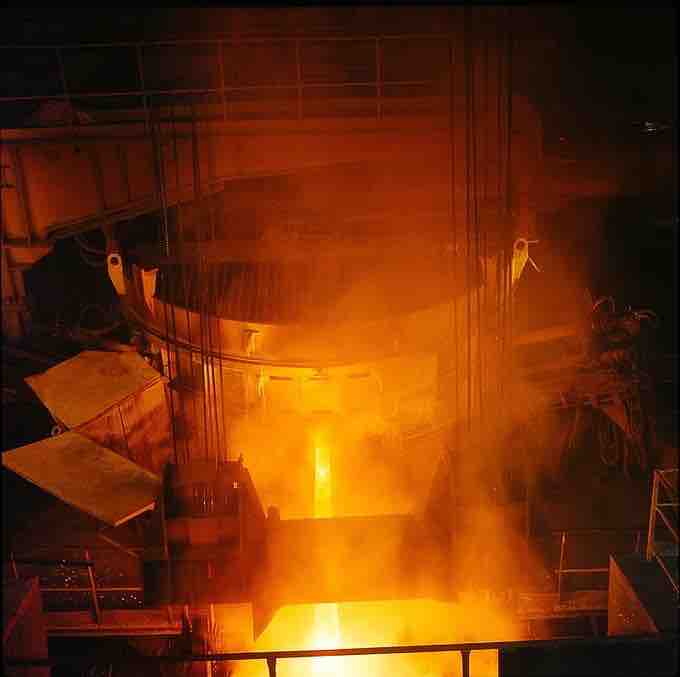
Electric Arc Furnace
An electric arc furnace (the large cylinder) is tapped.
The formation of slag, which floats on the surface of the molten steel, is an important part of steelmaking. Slag usually consists of metal oxides and acts as a destination for oxidized impurities. It functions as a thermal blanket, stopping excessive heat loss, and helping to reduce erosion of the refractory lining.
When the scrap has completely melted down and a flat bath is reached, another bucket of scrap can be charged into the furnace and melted down. Once the temperature and chemistry are correct, the steel is tapped out into a preheated ladle by tilting the furnace. For plain-carbon steel furnaces, as soon as slag is detected during tapping, the furnace is rapidly tilted back towards the deslagging side, minimizing slag carryover into the ladle.
HIsarna Steelmaking
The HIsarna steelmaking process is a process of primary steelmaking in which iron ore is processed almost directly into steel. The process is based on a new type of blast furnace called a Cyclone Converter Furnace, which makes it possible to skip the process of manufacturing pig iron pellets, a necessary step in the basic oxygen steelmaking process. Because it skips this step, the HIsarna process is more energy-efficient and has a lower carbon footprint than traditional steelmaking processes.
Refining
Refining consists of purifying an impure material, in this case a metal. In refining, the final material is usually chemically identical to the original, but purer. There are many different processes for refining, including pyrometallurgical and hydrometallurgical techniques.
Wrought Iron
The product of the blast furnace is pig iron, which contains 4-5 percent carbon and usually some silicon. To produce a forgeable product, a further process was needed, usually called "fining" rather than "refining. " Starting in the 16th century, this process was performed in a finery forge. At the end of the 18th century, it began to be replaced by puddling in a puddling furnace, which was, in turn, gradually superseded by the production of mild steel through the Bessemer process.
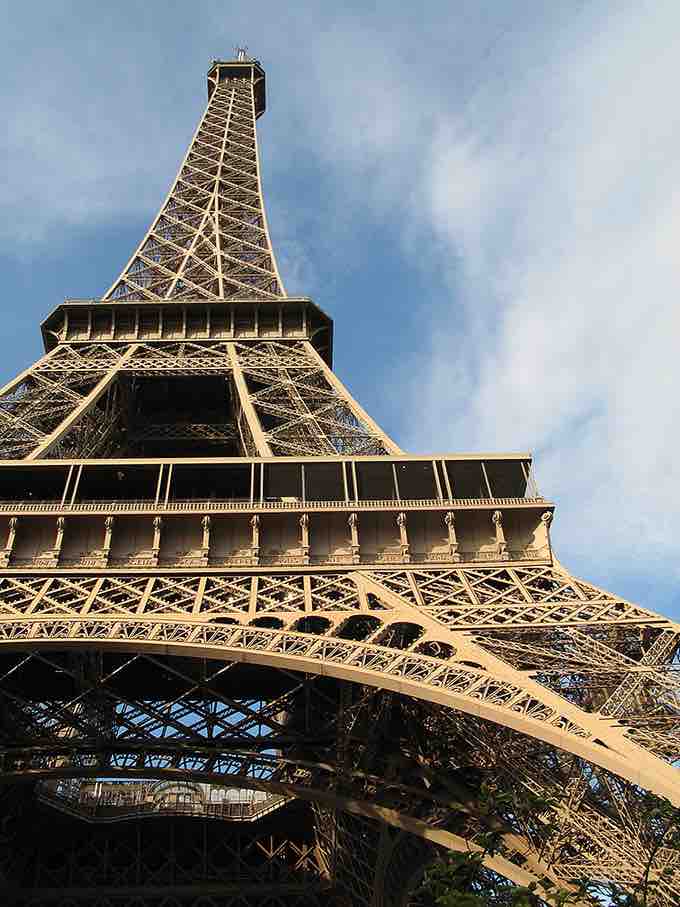
Eiffel Tower
The Eiffel tower is constructed from puddled iron, a form of wrought iron.
The term "refining" is used in a narrower context. Henry Cort's original puddling process only worked when the raw material was white cast iron, rather than the gray pig iron that was the usual raw material for finery forges. For the gray pig iron to be usable, a preliminary refining process was developed to remove the silicon. The pig iron was melted in a running-out furnace and then run out into a trough. This process oxidized the silicon to form a slag, which floated on the iron and was removed by lowering a dam at the end of the trough. The product of this process was a white metal known as finers metal or refined iron.